Bonjour Monsieur Gonnon, vous êtes en charge des applications mortiers et bétons pour le groupe OMYA International et votre témoignage à ce titre nous semblait utile pour apporter le regard d’un industriel sur ce sujet finalement assez peu connu dans la profession.
Pourriez-vous nous dire quelques mots sur OMYA et sur ses métiers ?
OMYA est une société familiale, producteur de charges minérales, et aussi distributeur de produits chimiques, mais notre cœur de métier est la production de carbonate de calcium, notre activité a débuté en 1884 en Suisse.
Des lors, le développement des carbonates de calcium micronisés s’est effectué sur les marchés du papier, de la peinture et du plastique. Au cours du temps, se sont développé le marché de la construction en particulier les mortiers et bétons, ainsi que d’autres segments tels que le traitement de l’eau, la pharmacie ou la cosmétique.
Le carbonate de calcium est un matériau présent dans beaucoup d’applications ; pour OMYA, cela représente 175 usines de production dans plus de 50 pays. La majorité des sites industriels sont certifiés ISO 9001 / 14001. Notons que Omya est pionnier pour ses carrières à être certifié ISO 14001.
Dans les marchés des mortiers et bétons, depuis plus de 20 ans, pour être au plus près des besoins techniques des clients et en capacité à développer des carbonates micronisés distribués sous la marque Betocarb ou Betoflow D, les maîtres mots sont la finesse, la dispersion, la pureté, la blancheur.
Il est important de rappeler que le producteur de calcaire industriel, s’appuie tout d’abord sur une qualité de gisements et ensuite sur une expertise des procédés de broyage et de séchage. Le calcaire est une roche sédimentaire et il existe de fait une grande diversité de roches, qui peuvent être tendres ou dures selon qu’elles proviennent d’un gisement de craie, de calcite, ou de marbre. La matière première conditionne donc le procédé et les propriétés du produit fini.
Donc si je comprends bien, la pureté du carbonate de calcium est un élément clé. Pouvez-vous nous en dire plus ?
La représentation des 3 pôles du calcaire tels que B. Haguenauer [paru dans Mines et Carrières en mars 1996], les définit : 1. Carbonates (réactivité chimique), 2. Quartz, feldespaths, micas (stabilité chimique), 3. Minéraux argileux et secondaires-pyrite (hydrophiles et gonflants), rend bien compte de cette problématique de pureté.
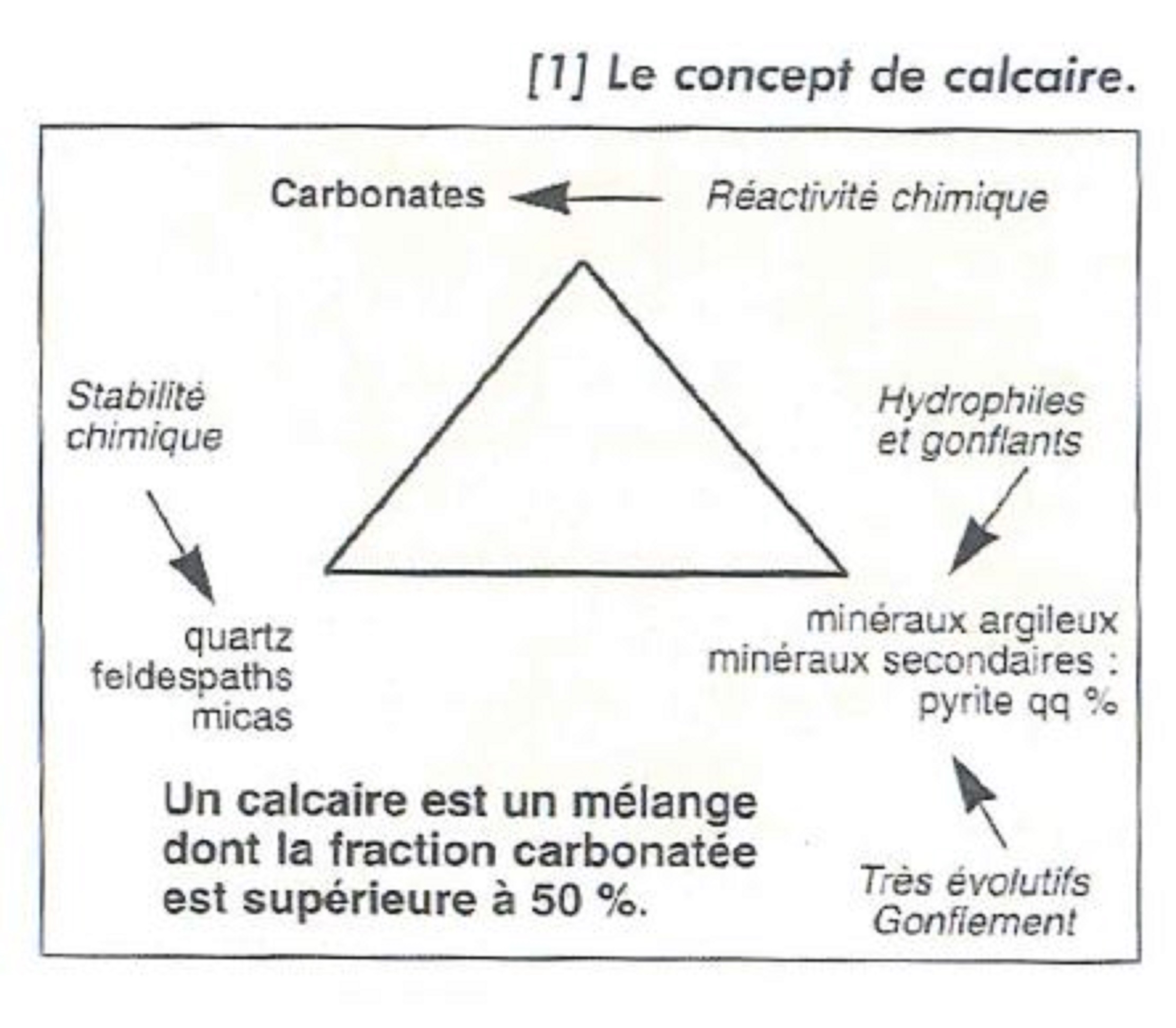
Extrait de : La localisation et l’utilisation économique optimale des ressources carbonatées d’une région / Bernard Haguenauer. In Mines et carrières – Industrie minérale, mars 1996.
Lorsque la proportion de carbonates est présente en force, les deux autres pôles ne sont plus qu’en petites proportions. C’est ainsi par la maîtrise de la qualité de la matière première que l’on diminue les interactions possibles des minéraux secondaires avec les chimies dispersantes et défloculantes dans les matrices cimentaires. Et c’est pourquoi la recherche de pureté maximale du matériau est primordiale dans la production des carbonates micronisés et cela d’autant plus que sa finesse est importante.
Pour exemple, dans les produits Betocarb® HP et Betoflow® D de la société OMYA, la teneur en chlorures et sulfates est de l’ordre de quatre décimales après la virgule, c’est dire leur faible proportion.
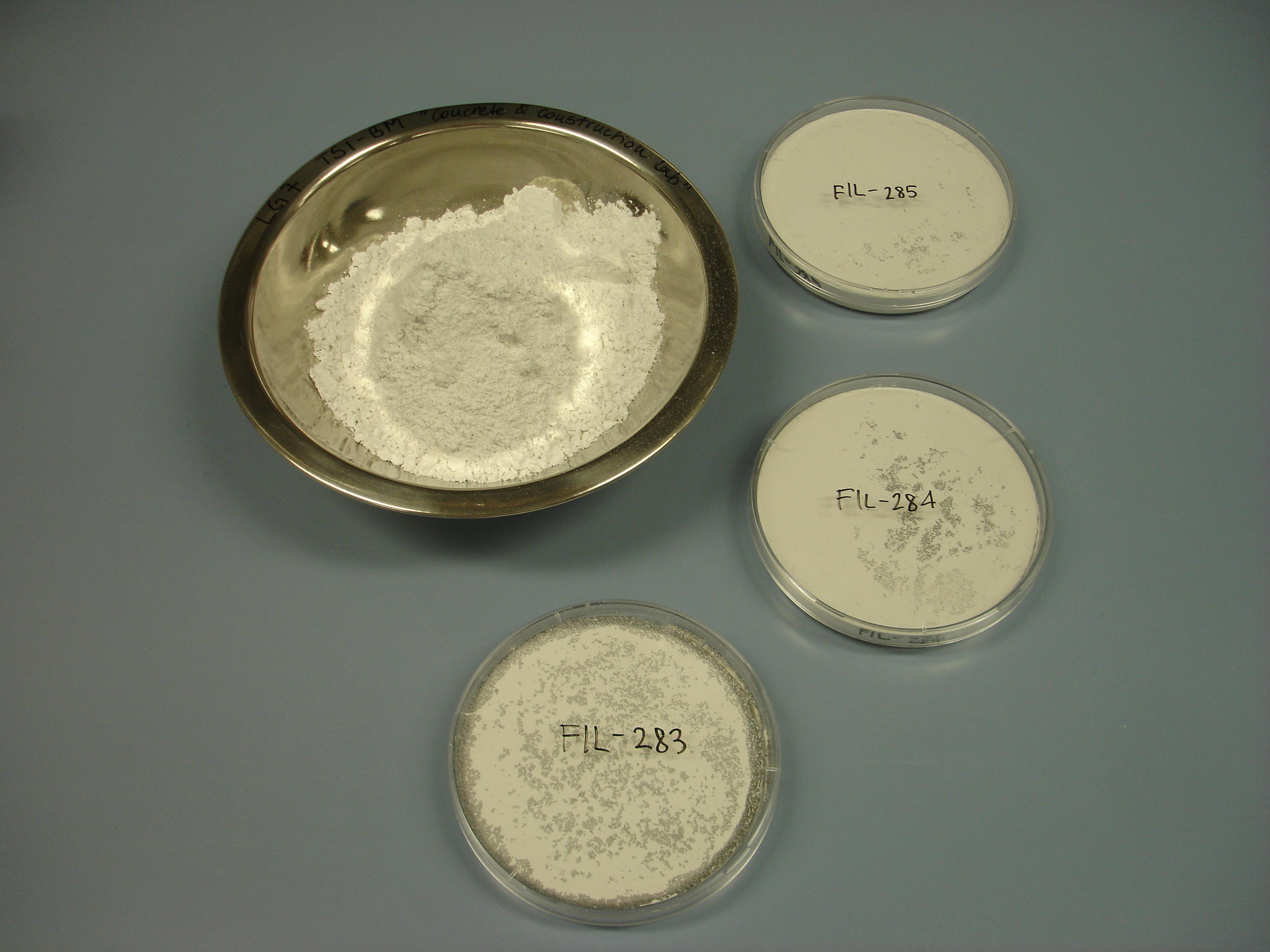
Source : OMYA
En matière de formulation et de performance des bétons, pouvez-vous maintenant nous éclairer sur le rôle du carbonate de calcium ?
De façon simplifiée, la contribution des additions calcaires se situe à deux niveaux : la première, d’ordre physique, est la participation d’un élément micronisé à la compacité de la matrice cimentaire, favorisant ainsi la consistance du mélange ; la deuxième, d’ordre chimique, est l’optimisation des performances mécaniques, notamment aux jeunes âges mais aussi à 28 jours, qui est d’ailleurs l’échéance retenue pour la mesure de l’indice d’activité. Mais aujourd’hui, pour l’ingénieur, le concept de calcaire est à compléter par l’opportunité de combiner des charges et additions minérales.
Cela va au-delà de l’idée de performance équivalente ou d’éco-béton et il n’est d’ailleurs pas question d’opposer les carbonates micronisés aux additions à propriété pouzzolanique tel que les laitiers vitrifiés ou les fumées de silice par exemple ; ce sont les notions de synergie, de leur capacité à être plus facilement dispersés dans un liquide aussi polaire que l’eau, et enfin de leur affinité avec les superplastifiants de nouvelle génération, qui vont gouverner les propriétés du mélange à l’état frais et à l’état durci. Dans cet objectif, nous avons d’ailleurs développé la méthode LG10 afin de pouvoir mesurer pour un ciment donné, l’activité d’une addition minérale seule ou combinée.
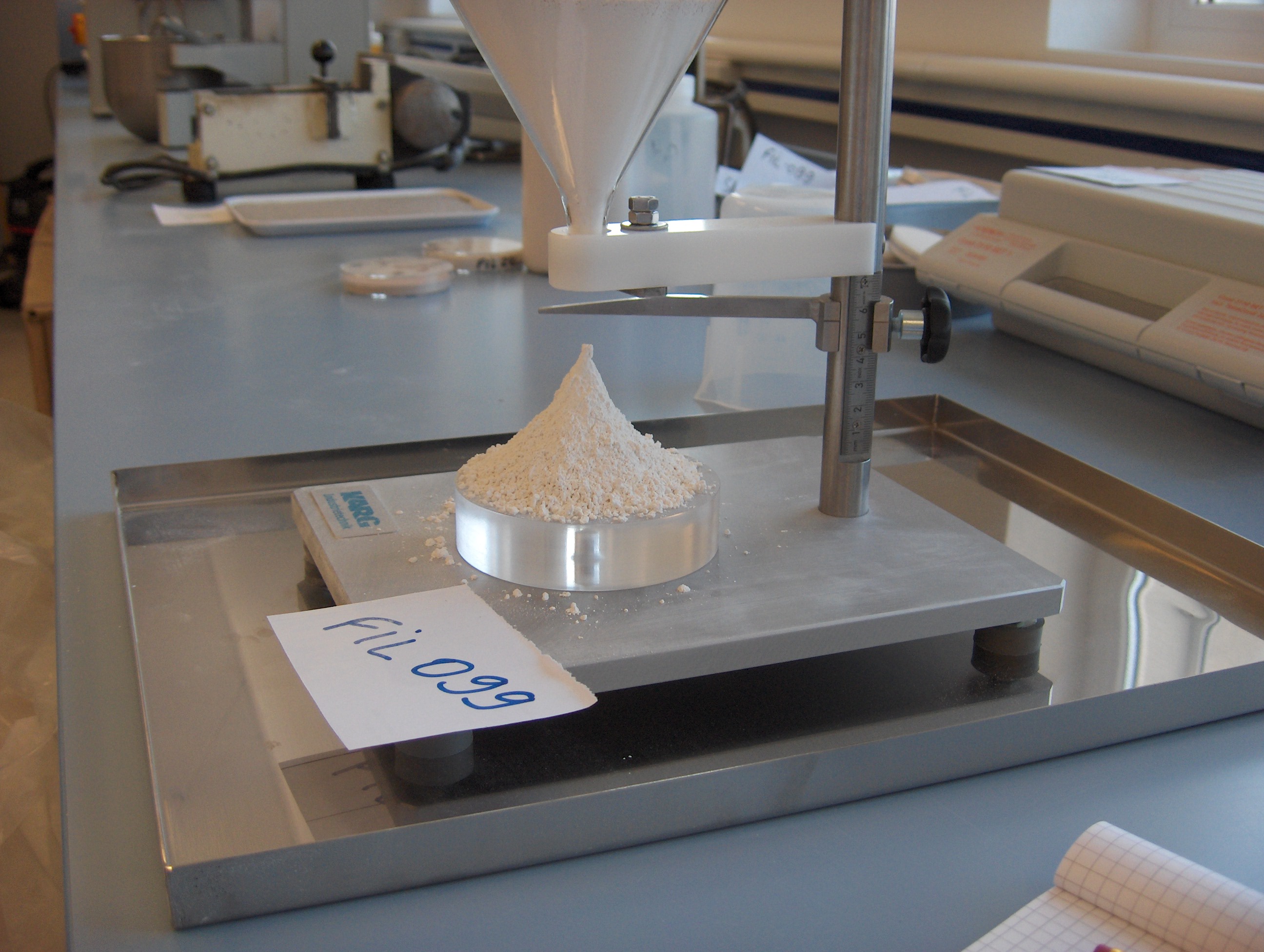
Source OMYA
Et qu’en est-il de l’impact environnemental de cette filière industrielle ? Peut-on l’évaluer ?
Depuis de nombreuses années, il existe une valeur relative au bilan carbone déclarée par l’Industrial Minerals Association (IMA), l’organisme qui représente l’ensemble des producteurs de matériaux naturels, qui est de 62 kg/tonne de GCT (General Consumption Tax) produit, mais il n’y a pas de valeur pour chacun des carbonates de calcium.
OMYA est certifié ISO 14001, et est extrêmement soucieux de l’aspect environnemental mais aussi santé de ses activités, tant du point de vue du maintien de la biodiversité, de la réduction des impacts visuels que de la santé des employés.
Venons-y maintenant… comment fabrique-t-on des produits aussi fins ?
La fabrication démarre du gisement qui, selon les contraintes existantes, peut se trouver ou non à côté de l’usine. La matière première arrive sous forme de blocs à l’usine et passe par une série d’étapes de fragmentation. De façon systémique, trois phases sont en œuvre : le broyage, la sélection, et le séchage. Dans le broyeur, on s’emploie à obtenir une taille de particules cible ; lors de la sélection, on enlève les particules qui ont atteint la taille recherchée, et on continue à broyer les autres. Enfin le séchage permet d’obtenir un produit dont la teneur en eau est inférieure à 1%.
Pour des applications industrielles telles que le plastique, des traitements de surfaces sont appliqués, qui confèrent au carbonate micronisé la propriétés d’hydrophobie ; pour l’industrie du papier, les carbonates sont broyés en phase aqueuse et livrés sous forme de slurry ou bien séchés.
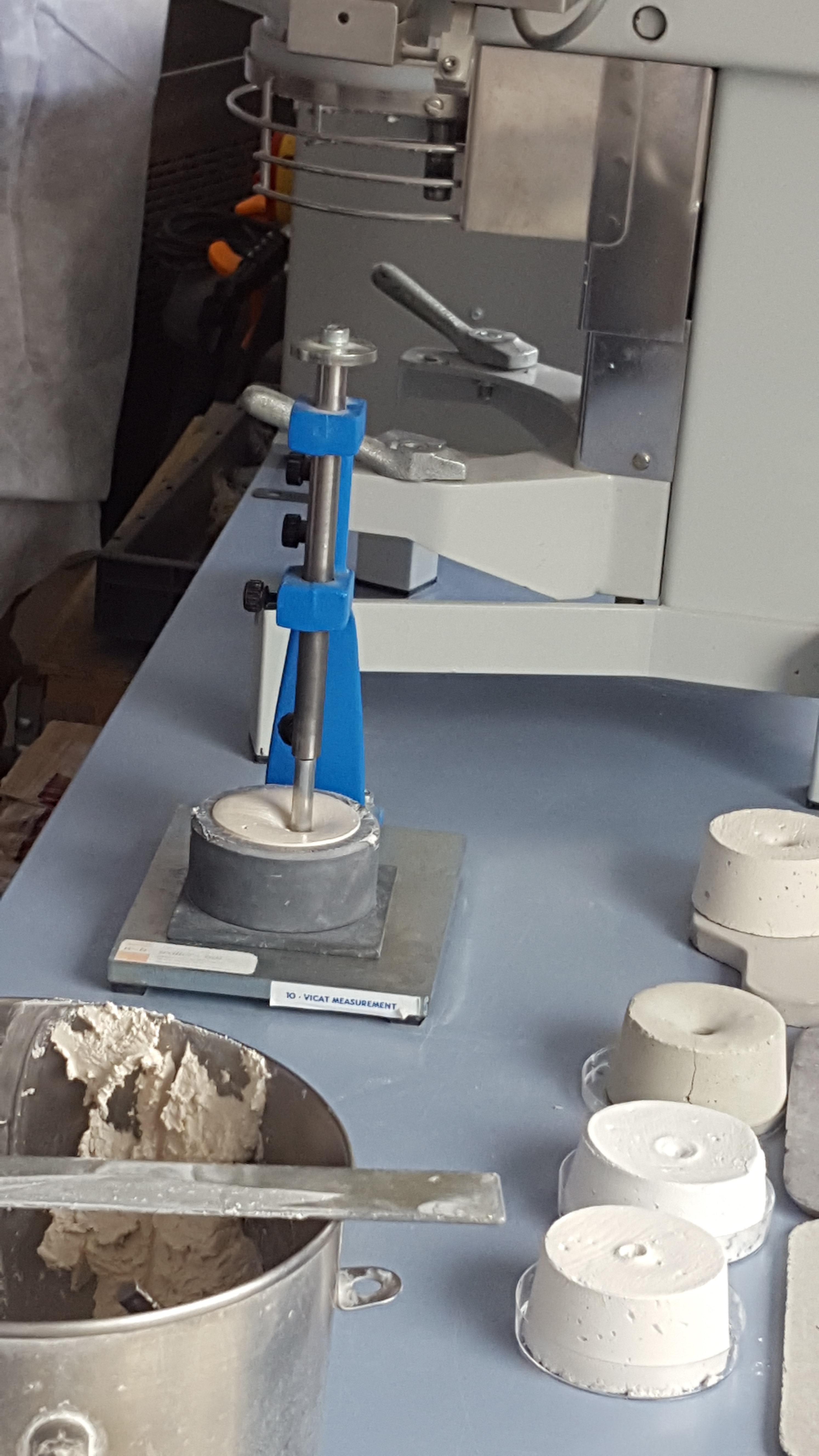
Source : OMYA
Qu’en est-il alors de la taille des usines et de l’outillage qui permettent d’obtenir une telle finesse du produit ? Y a-t-il une corrélation entre la taille de machines et la taille du produit final ?
Dès l’origine, la société OMYA a œuvré au développement de procédés industriels spécifiques. Ses compétences en interne sont dédiées à la maîtrise de toutes les étapes de la production de calcaires industriels ; ainsi, des premières tonnes de craie micronisée à aujourd’hui, la taille et la technologie des sites industriels a énormément évolué. Il est un fait que la taille et le conditionnement des calcaires micronisés conditionne la taille du dispositif industriel.
La qualité esthétique du béton a toute son importance … le carbonate de calcium peut-il jouer un rôle dans l’aspect de surface ?
Oui, et cela depuis longtemps car l’homme de l’art sait « qu’un béton bien plein avec une belle peau aura une belle performance ». Pratiquement, on cherche le point de saturation du carbonate de calcium, car on est dans l’idée de remplissage optimum. Ainsi, c’est l’indice des vides du squelette de la formulation qui gouverne le point de saturation en carbonate micronisé, et cela d’autant plus que la consistance de la pâte est fluide et que la taille du plus gros grain est faible.
Or, dès qu’on utilise le carbonate de calcium comme un plastifiant minéral, on améliore non seulement l’ouvrabilité et la stabilité mais aussi l’esthétique du produit fini. L’amélioration des parements se vérifie sur les produits de consistance « terre humide » tels que les blocs jusqu’au mortiers et bétons autonivelants. Dans le cas des mortiers et bétons formulés à base de ciment blanc, l’usage de calcaires micronisés blancs permet de renforcer la blancheur et l’homogénéité du produit final car l’optimisation de la compacité permet d’apporter ce que les peintres industriels nomment « du fond ». Dans le même thème, notamment pour les produits à forte valeur ajoutée tels que les BUHP, la performance des pigments dont le diamètre de l’ordre de 0.5 µ est améliorée par l’usage de carbonates ultrafins tels que le Betoflow® D ou le Betocarb® UF.
Par ailleurs il est à noter qu’un essai normé (essai LG_007 décrit en annexe B de la norme NF P18‑508) permet de vérifier si les additions minérales, filler ou fines des granulats peuvent présenter un risque de maculation des parement (oxydes ferriques, pyrite…). Cet essai consiste à formuler avec un dispersant puissant, un slurry de faible viscosité et de suivre visuellement la qualité du surnageant. Pratique, l’essai est couramment utilisé, par exemple pour la qualification des matériaux destinés à fabriquer des bétons blancs ou architectoniques. Cela confirme notre intérêt de maîtriser la qualité des fines, de leur régularité et de leur origine.
Finalement, comment définiriez-vous la place prise par le carbonate de calcium dans la composition d’un béton ?
Les fillers calcaires sont connus depuis de nombreuses années et la première norme addition calcaire (NF P 18-508) de 1995 était une étape qui permettait de le distinguer de la catégorie « fines », de la norme granulat de l’époque. Depuis, avec une contribution très significative de l’industrie de la chimie, la technicité des mortiers et des bétons a énormément progressé et nous voyons que la révision de la norme addition calcaire en 2011 a précisément complété les caractéristiques de finesse et de propreté.
Aujourd’hui, pour accompagner le marché de la construction dans le développement des mortiers et bétons techniques, l’usage des carbonates micronisés fonctionnels tels que Betocarb® HP ou Betoflow® D s’explique d’une part par le besoin du formulateur de maîtriser la rhéologie et la stabilité des mélanges mais aussi pour des raisons environnementales. Ce dernier élément, pas seulement en France, marque une évolution récente et significative, car l’ingénieur fait le choix du liant, qui peut être un ciment composé, combiné ou non avec un matériau à propriété pouzzolanique.
La place des carbonates de calcium micronisés industriels est dans tous les mélanges formulés avec un ciment et des matériaux pouzzolaniques, pour lesquels l’ingénieur souhaite optimiser la fluidité, la compacité, la résistance au jeune âge, la stabilité, l’homogénéité des parements et l’esthétique des éléments finis. Ainsi, selon les niveaux de résistance et de durabilité, il est possible de sélectionner un ou plusieurs carbonates de calcium micronisés.
Pascal Gonnon
Senior Application Manager
Concrete, Cement & Mortars
Technical Services & Innovation
Building Materials – Oftringen