Le ciment, la norme NF EN 197-1 en donne une définition :
» Le ciment est un liant hydraulique, c’est-à-dire un matériau minéral finement moulu qui, gâché avec de l’eau, forme une pâte qui fait prise et durcit par suite de réactions et de processus d’hydratation et qui, après durcissement conserve sa résistance et sa stabilité, même sous l’eau. «
La fabrication du ciment courant
Le constituant principal du ciment est le clinker. Il est obtenu par la cuisson d’un mélange composé généralement aux environs de 80% de calcaire (majoritairement composé de carbonate de calcium CaCO3) et de 20% d’argile mélange complexe et souvent hydraté de silice (SiO2), d’alumine (Al2O3) et d’oxyde de fer (Fe2 O3)).
Extraction, concassage et broyage
Les matières premières sont extraites des carrières. Les blocs extraits sont ensuite concassés sur le site même de la carrière à une dimension d’environ 50 mm.
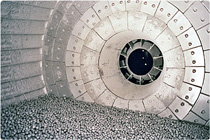
Intérieur d’un broyeur à boulets
Préparation du cru
Les morceaux de calcaires et d’argile sont broyés très finement et sont intimement mélangés pour donner le cru.
Deux techniques de fabrication sont utilisées : le mélange est préparé sous forme de poudre (c’est la voie sèche ou semi-sèche) ou sous forme de pâte (c’est la vois semi-humide ou humide).
La voie sèche est aujourd’hui la plus utilisée. La pratique de la préhomogénéisation affine considérablement le dosage du calcaire et de l’argile, par l’empilement de nombreuses couches des deux matières premières.
Au sortir de la préhomogénéisation, le mélange est broyé très finement pour donner ce cru dont nous venons de parler. Le cru est ensuite réhomogénéisé par fluidisation.
La composition du cru respecte généralement les proportions suivantes :
Composant du cru
|
Proportion
|
|
Carbonate de calcium (CaCO3) |
77 à 83 %
|
|
Silice (SiO2) |
13 à 14%
|
|
Alumine (Al2O3) |
2 à 4%
|
|
Alumine (Al2O3) |
1,5 à 3 %.
|
Cuisson du cru
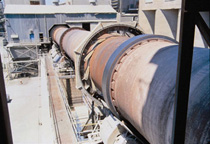
Four rotatif de cimenterie
Les installations de cuisson comprennent deux parties :
-1 La poudre est déversée dans un échangeur de chaleur dans lequel circulent en sens inverse les gaz très chauds qui s’échappent du four. Le cru y progresse jusqu’à l’entrée du four proprement et est donc préchauffé à une température d’environ 800°C quand il atteint l’entrée du four. Sa décarbonatation commence.
-2 Le cru pénètre dans un four rotatif légèrement incliné qui tourne à un rythme de 1 à 3 tour/mn. Ce four mesure de 60 à 90 mètres. Le cru, en entrant dans le four achève sa décarbonatation et chemine vers la zone de clinkérisation (1450°C).
A partir de 650°C , le carbonate de calcium du calcaire subit une décarbonatation (CaCO3 – -> CaO + CO2). On obtient alors de la chaux vive (CaO) accompagnée d’un important dégagement gazeux (CO2).
La chaleur sépare l’argile en silice (SiO2), en alumine (Al2O3) et en oxyde de fer (Fe2O3).
A partir de 1300°C les réactions de clinkérisation se produisent :
Oxyde de fer (Fe2O3) + alumine (Al2O3) + oxyde de calcium (CaO) –> aluminoferrite tétracalcique (Ca4Al2Fe2O10).
Alumine (Al2O3) + chaux vive (CaO) –> aluminate tricalcique (Ca3Al2O6).
Ces deux composés nouvellement formés constituent la phase liquide du mélange . Celui-ci progresse vers la partie la plus chaude du four. La silice (SiO2) et la chaux vive (CaO) réagissent entre-elles :
Silice (SiO2) + chaux vive (CaO) –>silicate bicalcique (Ca2SiO4)
S’il reste de l’oxyde de calcium (CaO) qui n’a pas encore réagi, la réaction peut se poursuivre :
Silicate bicalcique (Ca2SiO4) + chaux vive (CaO) –>silicate tricalcique (Ca3SiO5)
Broyage du clinker
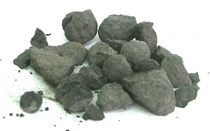
Granulés de clinker prêt à être broyé
A la fin de la cuisson, la matière est brusquement refroidie. Elle se présente alors sous forme de granules. Il s’agit du clinker dont la composition est la suivante :
Nom cimentier
|
Formule
|
Min.
|
Max.
|
|
Alite (silicate tricalcique) |
Ca3SiO5
|
45.0 %
|
79.7 %
|
|
Bélite (silicate bicalcique) |
Ca3SiO4
|
5.7 %
|
29.8 %
|
|
Aluminate tricalcique |
Ca3Al2O6
|
1.1 %
|
14.9 %
|
|
Aluminoferrite tétracalcique |
Ca4Al2Fe2O10
|
2.0 %
|
16.5 %
|
|
Chaux libre |
CaO
|
0.6 %
|
2.8 %
|
Finement broyé avec du gypse (destiné à réguler la prise), le clinker donne le ciment Portland.
D’autres ciments sont obtenus en ajoutant à cette phase de broyage divers constituants : laitier granulé de haut fourneau, cendres volantes, fillers, schistes calcinés, qui sont des matériaux pouzzolaniques.
La composition chimique du ciment garantit ses qualités ; des analyses sont donc effectuées sur des échantillons prélevés régulièrement tout au long du procédé de la fabrication. On analyse également les matières premières et les combustibles afin de connaître leur teneur en différents composés et de pouvoir ainsi les doser.
On analyse également les matières premières et les combustibles afin de connaître leur teneur en différents composés et de pouvoir ainsi les doser. Ces analyses sont d’autant plus importantes que la fabrication du ciment emploie aujourd’hui des produits de recyclage, pour les matières premières et pour les combustibles
Lecture complémentaire :
Les voies de réductions des émissions de CO2 de l’industrie cimentière…
Entretien avec Paul Acker, Directeur scientifique du Centre de recherche de la Société Lafarge (Lettre d’information du LERM n° 10 )