Monsieur Hallopeau, vous êtes expert corrosion et protection cathodique chez Freyssinet, pouvez-vous nous expliquer le principe du traitement électrochimique du béton ?
Volontiers, mais, auparavant, un rapide rappel des pathologies auxquelles peuvent s’appliquer un traitement électrochimique nous permettra de comprendre les enjeux de ces traitements et nous introduira aux principes de leur fonctionnement et de leur mise en œuvre.
C’est de bonne méthode… Allons-y !
Les traitements électrochimiques s’appliquent aux bétons armés lorsque la corrosion des armatures est à craindre ou à réparer suite notamment à deux pathologies la carbonatation du béton d’enrobage et/ou la pénétration des ions chlorures (dans les deux cas jusqu’à la profondeur des armatures).
La carbonatation est inéluctable dans le temps. Son vecteur est le CO2 de l’air qui réagit avec les hydrates du béton formant un front d’avancement. Lors de cette réaction, l’alcalinité diminue, le pH initial du béton voisin de 13 devient égal à 9 et les armatures peuvent alors se corroder de manière généralisée.
Les ions chlorures proviennent essentiellement des atmosphères marines ou des sels de déverglaçage en ville et en montagne et conduisent à une corrosion localisée des armatures que l’on appelle également piqûres.
Lorsque les armatures se retrouvent dans un béton contaminé de manière non uniforme, elles peuvent se corroder dans certaines conditions et cela nécessite de l’eau et de l’oxygène.
Les produits de corrosion du fer qui se forment ont des incidences sur la structure : perte de section de l’acier, diminution de l’adhérence acier/béton et fissuration du béton d’enrobage (voire épaufrure). La corrosion des aciers du béton armé présente un risque structurel pour l’ouvrage (diminution de capacité portante) mais également un risque à l’usager en cas de chute de débris de béton.
Que peuvent apporter les traitements électrochimiques pour des bétons ainsi atteints ?
Les traitements électrochimiques sont spécifiques de chacune des pathologies.
Le traitement de réalcalinisation consiste à remonter l’alcalinité du béton à l’interface armature/béton pour diminuer sensiblement la réaction de corrosion.
Le traitement d’extraction des ions chlorures, a, lui, pour objectif d’extraire les ions chlorure du béton d’enrobage pour diminuer le risque de corrosion des armatures.
Pour des structures fortement exposées à ces polluants, il est recommandé de combiner leur réparation avec l’application d’une protection cathodique par courant imposé, qui est donc un traitement non plus temporaire mais permanent, et seul procédé capable de fournir aux structures les courants de protection nécessaires de façon durable.
L’intérêt de ces techniques tient dans le fait qu’elles opèrent un traitement complet des aciers de la structure, contrairement à une réparation localisée (purge et ré-enrobage) dans un béton qui reste largement pollué et dont la dégradation va se poursuivre sur le pourtour de la zone réparée par effet d’anode induite.
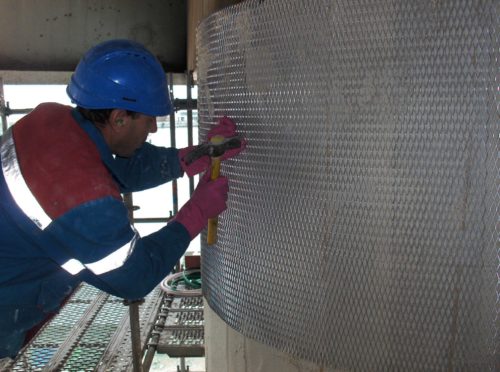
Mise en place du treillis métallique (anode)
Pouvez-vous nous décrire le dispositif technique des traitements ?
Pour ces deux traitements le principe est le même : il faut protéger le réseau d’armatures qui constituera donc la cathode. L’anode sera composée d’un treillis métallique encapsulé dans une couche de pâte de cellulose appliquée à la surface du béton. La pâte de cellulose sert de réservoir à une solution alcaline renouvelée durant toute la durée du traitement afin d’assurer la circulation du courant. Le réseau d’armatures continu du béton et le treillis sont reliés à une source de courant continu qui, sous une tension maxi d’environ 40 V pour éviter tout risque humain, va délivrer des densités de courant de l’ordre de l’ampère par m² d’acier.
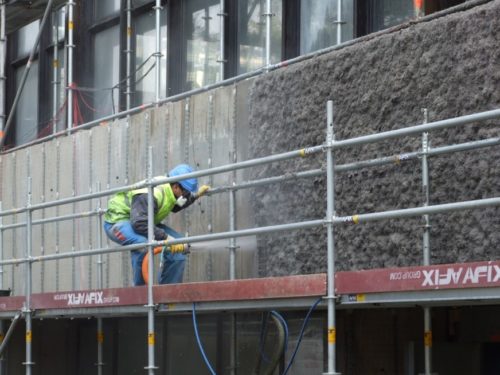
Projection de la pâte de cellulose
Quelle est la durée moyenne de ces traitements ?
Il faut compter 2 à 3 semaines pour la réalcalinisation et 4 à 8 semaines pour l’extraction des ions chlorures.
Pendant les travaux, les tensions sont contrôlées et des échantillons de béton sont prélevés au droit des aciers pour analyser l’alcalinité et la teneur en ions chlorures.
Des mesures électriques indirectes, cartographie de potentiel ou de résistance de polarisation, peuvent également démontrer une application correcte du traitement puis une diminution (plutôt qu’arrêt) de l’activité de corrosion. La complémentarité de ces résultats de mesures déterminent la poursuite ou non du traitement.
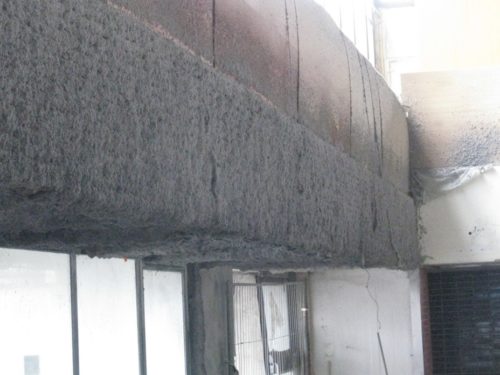
Poutre prête pour le traitement électrochimique
Quel est le niveau d’efficacité de ce type de traitement ?
Le niveau d’efficacité nous est donné par les mesures que je viens d’évoquer.
Pour ce qui concerne la réalcalinisation, la polarisation induite sur les armatures va générer des ions hydroxyles qui vont faire remonter l’alcalinité du béton et donc le pH, ce que révèlera le test à la phénophtaléine.
Pour ce qui concerne les chlorures, les carottes de béton prélevées doivent présenter une teneur en ions chlorures inférieure à 0,4 % de la masse du ciment à la profondeur des armatures selon la norme EN 206. Même si aujourd’hui ce seuil et sa valeur sont encore fortement discutés il est admis que c’est une concentration critique à partir de laquelle la probabilité d’amorçage de la corrosion des aciers est réglementairement élevée.
Dans un environnement où le béton restera exposé au CO2 et/ou aux ions chlorures , il sera parfois pertinent de prévoir, en complément du traitement, l’application d’une protection en surface du parement (imprégnation hydrophobe, liant hydraulique modifié LHM, …).
Ces traitements électrochimiques connaissent-ils des limites ?
Les méthodes électrochimiques pour des densités de courant de l’ordre de l’ampère par m² d’acier sont contre-indiquées pour les ouvrages précontraints dont les armatures peuvent être fragilisées par l’hydrogène dégagé par la réaction de réduction de l’eau.
Par ailleurs, l’ajout d’alcalins lors du traitement impose une étude préalable sur la nature des granulats au regard d’éventuels risques d’alcali-réaction. Enfin, la réalcalinisation, en présence de sulfates pourrait générer des composés expansifs.
Lorsque le béton est contaminé au-delà du premier lit d’armature, il convient alors d’appliquer une protection cathodique par courant imposé dont la conception et la mise en œuvre doivent être réalisées par du personnel certifié (on en reparlera un peu après).
Avez-vous en mémoire quelques chantiers marquants ?
Oui, remontons à 2003, si vous le voulez bien… Il s’agit d’extraire les chlorures des balcons d’un bâtiment résidentiel de Marseille, La Grande Corniche, exposé aux chlorures marins. Le chantier est donc un chantier de déchloruration électrochimique. Nous faisons alors le choix d’un système galvanique, sans générateur développé par Freyssinet et appelé procédé Regebeton : le courant est débité par couplage galvanique entre un treillis aluminium, qui sert d’anode sacrificielle, et l’acier des armatures qui joue le rôle de cathode.
En 2010, nous traitons la Piscine Helios à Charleroi en Belgique : le chantier dure 7 mois. Il s’agit de traiter intérieurement 400 m² de poteaux et poutres en 2 phases : extraction des chlorures suivie d’une réalcalinisation. A l’extérieur 2 100 m² de murs sont également traités en réalcalinisation.
En 2011, un chantier original nous est proposé : les 17 piles de fondation de la résidence Monte-Carlo Star à Monaco, soumises aux embruns marins, doivent changer de destination par création d’un lieu clos sur cet espace. Les piles, d’un diamètre de 1,8 m, sont donc traitées par application du procédé Freyssinet Regebeton d’extraction des chlorures sur une surface de 400 m2.
Depuis 7 ou 8 ans la demande en extraction des chlorures est faible, alors qu’il s’agit d’une technique fiable et dont l’efficacité peut être démontrée de manière quantitative. De plus elle offre l’avantage par rapport à un simple patch repair de ne pas induire d’effet d’anode induite. La réparation serait alors plus durable.
Comment expliqueriez-vous ce phénomène ?
Les réparations à base d’électricité ne sont peut-être pas intégrées (encore) à la culture du génie civil et sans doute manquons-nous d’états de l’art convainquant comme ont su en rédiger les experts américains de la National Association of Corrosion Engineer (NACE).
Vos pratiques sont pourtant encadrées par des normes…
C’est exact et ceci de façon récente : la spécification technique sur FD/CEN/TS 14038-1, qui traite de réalcalinisation, date de 2004 et est devenu une norme européenne (EN 14038-1) en 2016 et la spécification technique FD/CEN/TS 14038-2, qui date de 2011, deviendra aussi une norme européenne en 2018.
Ces normes, de mon point de vue, sont sujettes à discussions car elles ne définissent pas réellement de critères à respecter : pour la quantité de charge, la durée de traitement, la densité de courant applicable, la taille des zones, seuls des seuils maxima sont définis. Ce flou n’aide pas le maître d’œuvre dans la rédaction d’un cahier des charges aux attendus clairs et intelligibles : donner l’assurance, par exemple, que le traitement respecte une mise en œuvre sécurisée d’un point de vue électrique, que les opérations de contrôle de l’efficacité du traitement sont bien spécifiées, etc.
Comment voyez-vous l’avenir des solutions électrochimiques ?
Cet avenir passe par la poursuite de la recherche, car les limites que nous pouvons rencontrer ne sont pas seulement économiques, elles sont également technologiques. Depuis les années 2000, des recherches au laboratoire et sur le terrain ont été menées par l’IFSTTAR (Institut Français des Sciences et des Technologies du Transport, de l’Aménagement et des Réseaux) anciennement le LCPC sur la protection cathodique, galvanique ou par courant imposé, et sur les traitements électrochimiques dont nous venons de parler. Malgré leur efficacité, ces techniques sont restées assez peu utilisées.
La recherche néanmoins se poursuit : ainsi une thèse a été soutenue à l’IFSTTAR le 3 octobre dernier sur ce beau sujet : « Processus de corrosion et de réparation par traitement électrochimique d’extraction des ions chlorure dans les bétons armés doublement contaminés : carbonatation et chlorures »…
D’un autre côté, le CEFRACOR (Centre Français de l’Anticorrosion) poursuit depuis 2014 ses travaux pour la certification des personnels en protection cathodique secteur acier dans le béton armé qui a vu sortir un peu moins de 60 candidats certifiés au niveau technicien et 3 candidats certifiés au niveau expert. Ces activités nécessitent en effet du personnel compétent selon la norme EN ISO 15257 qui est l’occasion, pour la profession, de se structurer, et surtout l’assurance pour les maitres d’ouvrage d’avoir à tous les stades, de la conception à la réalisation, des intervenants dont les compétences ont été éprouvées.