C’est à la fin du 19e siècle qu’on inventera le ciment d’aluminates de calcium pour remplacer le ciment Portland dans les bétons de structure exposés aux attaques sulfatiques. Depuis plus d’un siècle, ce ciment, en fonction des périodes et des pays, a connu plusieurs appellations différentes comme ciment à haute teneur en alumine, ciment alumineux, ciment fondu, etc.
Outre sa résistance aux sulfates, le ciment d’aluminates de calcium a montré de nombreuses particularités : un durcissement très rapide et des qualités qui lui permettent de résister à des conditions extrêmes qui peuvent même être associées entre elles : abrasion sévère, attaque acide, attaque bactérienne, températures élevées, cycles thermiques et hydriques, cycles de gel-dégel.
Le ciment alumineux peut atteindre, en 24 h, une résistance équivalente à celle d’un ciment Portland à 28 jours. La rapidité du durcissement du ciment d’aluminates de calcium l’a naturellement recommandé pour des applications de préfabrication, et ses qualités de résistance l’ont destiné à des emplois en conditions environnementales et thermiques particulièrement sévères.
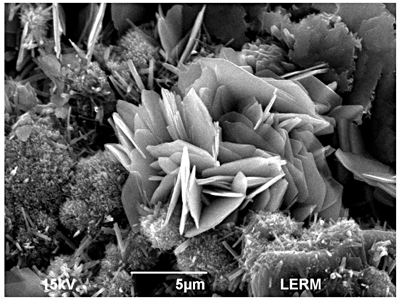
Aluminates de calcium prises avec le MEB . Tous droits réservés LERM 2010
Constituants et hydratation du ciment d’aluminates de calcium et phénomène de conversion
Le ciment alumineux est obtenu par fusion d’un mélange de calcaire (CaCO3) et de bauxite (Al2O3), puis par broyage du produit ainsi obtenu.
Le principal constituant du ciment d’aluminates de calcium est l’aluminate monocalcique (CaO Al2O3). Ses autres constituants sont les aluminoferrites de calcium, le silicate bicalcique et le silico-aluminate de calcium.
Compte tenu de son constituant principal, l’hydratation du ciment d’aluminates de calcium produit des aluminates de calcium hydratés et du trihydrate d’alumine insoluble, sans libérer de portlandite. C’est cette absence de portlandite qui lui confère sa résistance à de nombreux agents agressifs.
A une température inférieure à 30°C, l’hydratation du ciment d’aluminates de calcium commence par la formation d’hydrates hexagonaux métastables
(CAH10 et C2AH8+AH3). Avec l’élévation de la température, les hydrates hexagonaux se transforment en hydrates cubiques stables (C3AH6+AH3). Cette évolution inévitable est connue sous le nom de conversion et que la température des constituants lors du gâchage (eau, granulats, ciment) soit contenue.
Dans les bétons à base de ciment d’aluminates de calcium, du fait des différences de densité entre hydrates hexagonaux et cubiques, la conversion s’accompagne d’une augmentation de la porosité et d’un affaiblissement notable de la résistance. Du fait de ce phénomène de conversion, la norme NF EN 14647 précise, dans son Annexe A consacrée à l’emploi du ciment d’aluminates de calcium dans les bétons et les mortiers, que seule la résistance minimale après conversion doit être prise en compte.
Nous traiterons, dans notre prochaine lettre d’information (n°18) consacrée aux bétons spéciaux, des particularités des bétons à base de ciment d’aluminates de calcium.
(Zoom sur Le phénomène de conversion).
Bibliographie
– Norme NF EN 14647 (décembre 2006) : Ciment d’aluminates de calcium – Composition, spécifications et critères de conformité
– La durabilité des bétons, Bases scientifiques pour la formulation des bétons durables dans leur environnement, sous la dir. de Jean-Pierre Ollivier et Angélique Vichot, Presses de l’Ecole nationale des Ponts et Chaussées, 2008.
– M. Scrivener and A. Capmas. Calcium aluminate cements, in Lea’s Chemistry of cement and concrete. Arnold, 1998.